EVSE Overview
The Electric Vehicle Supply Equipment (EVSE) consists of all the equipment needed to deliver electrical energy from an electrical source to an electric vehicle’s battery (EV). The EVSE communicates with the EV to ensure that the charging coupler is securely connected to the vehicle receptacle before supplying a safe flow of electricity. There are two types of EVSE’s, the first one is an AC EVSE which supplies AC power to the vehicle, where the vehicle’s on-board charger converts the power from AC to DC to charge the batteries. The 2nd type— DC fast charging— provides DC electricity directly to the vehicle’s battery.
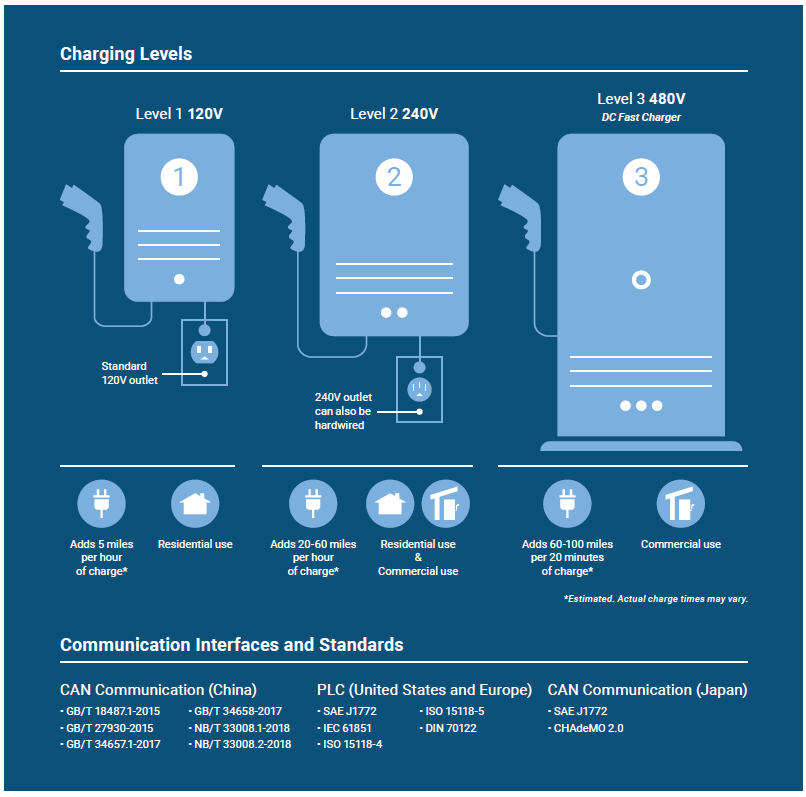
Overview of the Chroma AC Chargers
- Level 1 Chargers – The AC L1 chargers deliver single or 3-phase AC power to the EV OBC, and take 8-12 hours to charge a battery.
- Level 2 Chargers – AC Level 2 chargers are stationary chargers that are hard-wired to an electrical power supply like a breaker box. These chargers also provide AC power to the OBC for conversion to DC power to charge the battery. These chargers deliver twice as much power so they take half as long to charge as compared to the L1 chargers—charge time for these Level 2 chargers is 4-6 hours. Last but not the least, is the DC fast charger, which has its own on-board charger to convert the incoming AC power to DC power. That DC power is then delivered through the coupler directly to the DC battery on the vehicle.
- Level 3 Chargers – Level 3 DC fast chargers can charge a battery to 80% in 30 minutes or less.
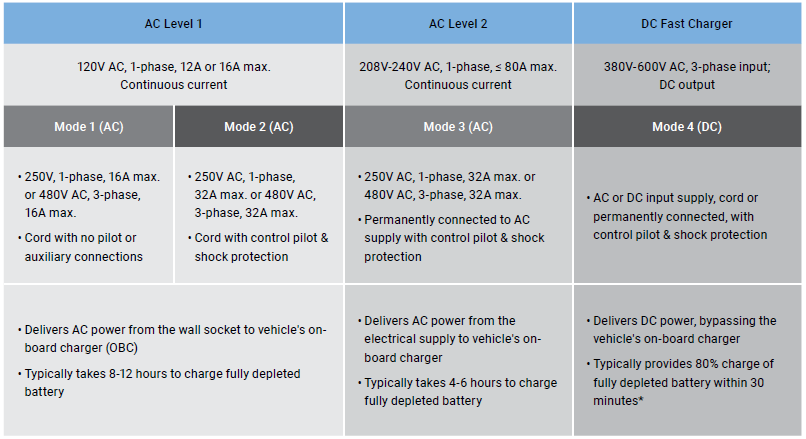
EVSE Standards Geography
EVSE standards are in general, based on geographic location. While the USA and Europe support SAE, ISO, and DIN standards, which are very similar, China and Japan have requirements that are unique to their location. A majority of the EVSE installations globally, are DC fast chargers that utilize CANbus communication and follow GBT standards. China is far ahead of the rest of the world in regards to establishing an EVSE charging infrastructure.
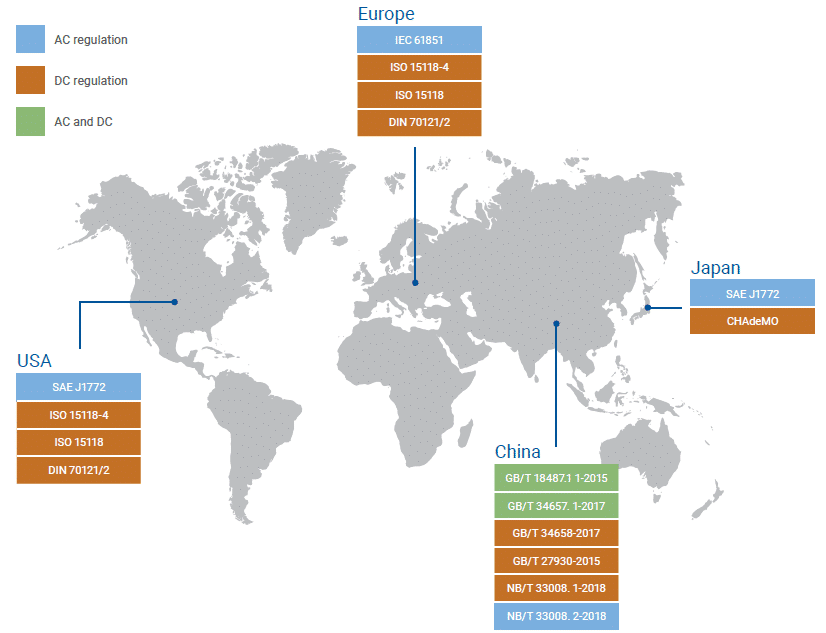
Coupler Interface by Region

The connectors are level and region dependent. Featured here are the different charging
interfaces available worldwide, which can be roughly divided into four regions: North America, Japan, European Union, China and a specialty connector used by Tesla.
EVSE Standards
SAEJ1772 (AC/DC)
SAE J1772 is a North American standard for electrical connectors for electric vehicles. It covers the general physical, electrical, communication protocol, and performance requirements for the electric vehicle conductive charge system and coupler (AC Only). The intent of this standard is to define a common electric vehicle conductive charging system architecture including the operational requirements and the functional and dimensional requirements for the vehicle inlet and mating connector.
ISO 15118 (AC/DC CCS1/CCS2)
ISO 15118 is an international standard that outlines the digital communication protocol that an electric vehicle (EV) and charging station should use to recharge the EV’s high-voltage battery. As part of the Combined Charging System (CCS), ISO 15118 covers all charging-related use cases across the globe. This includes wired (AC and DC) and wireless charging applications and the pantographs that are used to charge larger vehicles like buses.
DIN 70121 (DC CCS1/CCS2)
The German technical specification DIN SPEC 70121 is based on an early, unpublished version of the ISO 15118 standard and defines digital communication between an electric vehicle and a DC charging station. DC stands for direct current, which means DIN SPEC 70121 covers only the DC charging mode whereas ISO 15118 covers both AC and DC charging modes.
This means that a charging station that only supports ISO 15118 cannot charge an EV that only speaks DIN SPEC 70121. But if the EV is able to speak both dialects, then it can be used with either charging station—the same holds true on the EVSE side, if the EVSE can speak both ISO and DIN spec, then it can be used with both EV’s.
Another key distinction between ISO 15118 and DIN SPEC 70121 is that the latter does not support Plug & Charge, meaning: no secured communication via Transport Layer Security (TLS), no digital certificates, and no XML-based digital signatures so authenticity and data integrity can’t be ensured. Also, no smart charging is possible via DIN SPEC 70121, meaning: you can’t send charging schedules to the EV to make it charge in a smarter, more grid-friendly way.
DIN SPEC 70121 was created as an interim solution to get the market up and running until ISO 15118 was released. In reality, DIN spec’s days are numbered, as ISO 15118 and its wide range of additional features are fast becoming the industry standard.
EV Charging System Overview
There are two types of electric vehicle supply equipment: AC EVSE and DC EVSE. For an AC EVSE, the power will pass through the OBC where it is converted to DC power to charge the battery. Because the power is essentially consumed during conversion, the charging speed is slow, typically taking 4-12 hours to fully charge a battery.
DC EVSE, or commonly referred to as the DC Fast Charger is where AC power is converted to DC power at the EVSE and it charges the battery directly, which typically results in a charge time of 20 to 30 minutes. Power always needs to be converted from AC to DC when charging an electric vehicle; thus the technical difference between AC charging and DC charging is whether the power gets converted outside or inside the vehicle.
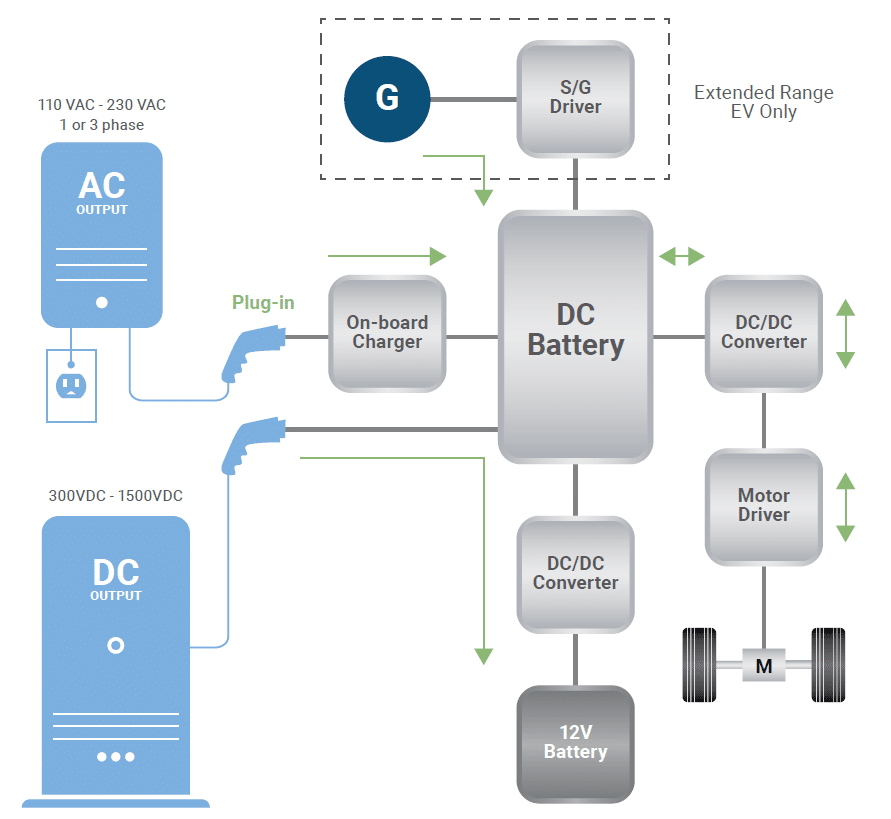
EVSE Test System
In regards to testing a L1 or L2 EVSE, there are typically three major components including: a grid simulator which act as the power input to the EVSE from the grid. An AC EVSE control unit provides the Control Pilot and Proximity detection signals back to the EVSE, basically emulating the EV side of the transaction. The last major component is an AC load to accept energy from the EVSE as if it were an OBC. Standard test cases show two types of tests for AC EVSE’s- one is related to power, whether it be in or out, and the other is related to communication, or in this case, the CP signal.
Key ATE Components for AC L1/L2
61815 Key Features
- Output Power: 61809: 9kVA, 61812: 12kVA, 61815: 15kVA
- Output voltage: 0~350V
- Output frequency: 30Hz~100Hz / DC
- High Power Density 15kVA in 3UH
- User selectable single phase or three phase output
- Full 4 quadrant, fully regenerative up to 100% of output current rating
- Programmable slew rate settings for voltage and frequency
- Synchronize TTL signal of voltage changing
- LIST, PULSE, STEP mode functions for testing Power Line Disturbance (PLD) simulation
- Harmonics, inter-harmonics waveform synthesizer AC EVSE Charging Test Items
AC EVSE Charging Test Items
- Control Pilot Signal
- Abnormal Control Pilot Signal
- Current Capacity
- Couple Disconnection
- AC Energy Transfer
- Harmonic Distortion Immunity
- Voltage Interruption and Variation
- Input Output Test
Test Standards
- SAE J1772
- GB/T 18487.1
- IEC 61851-1
AC L1/L2 EVSE Test System
Chroma’s EVSE test system features an AC source, or a grid simulator feeding input power to the EVSE. The EVSE is then interfaced to the Chroma AC EVSE control unit by connecting the charger gun to the socket on the EVSE control unit. Chroma has developed a 3-in-1 AC EVSE control unit that is capable of interfacing to the regional couplers—SAE, GBT, or IEC connector standards.
AC Load
The last major component is the AC load, which acts as the OBC to receive power from the charger. The test system requires a digital multimeter to measure the control pilot signals from the EVSE as well as an oscilloscope to measure the timing of those signals as well as other time based events that happen during the charging process. All related standards, SAE IEC GB, require timing certain events that need to take place within a certain amount of time.
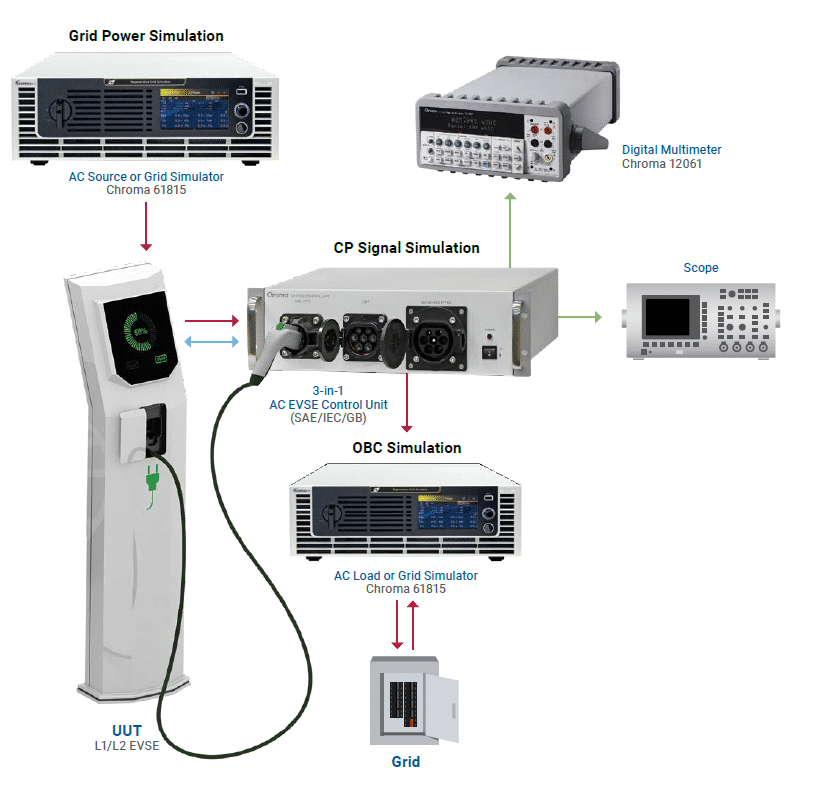
Understanding which test cases are advantageous or necessary to run is very important. Are you looking to verify that the EVSE can communicate to the EV and start the charging process? If that is the case, you could get by with facility or grid power and integrate a very small AC load with the Chroma EVSE control unit. While some customers have in-depth knowledge of their testing needs, others need some consulting to make sure that they are not buying more than they need, or to make sure that their system is flexible enough so that it can be upgraded in the future if their testing requirements are expanded.
MDL Technologies has the technical background to help you understand which tests you will need to run as well as the required instrumentation to provide a system that will meet your needs today and be easy to upgrade in the future.
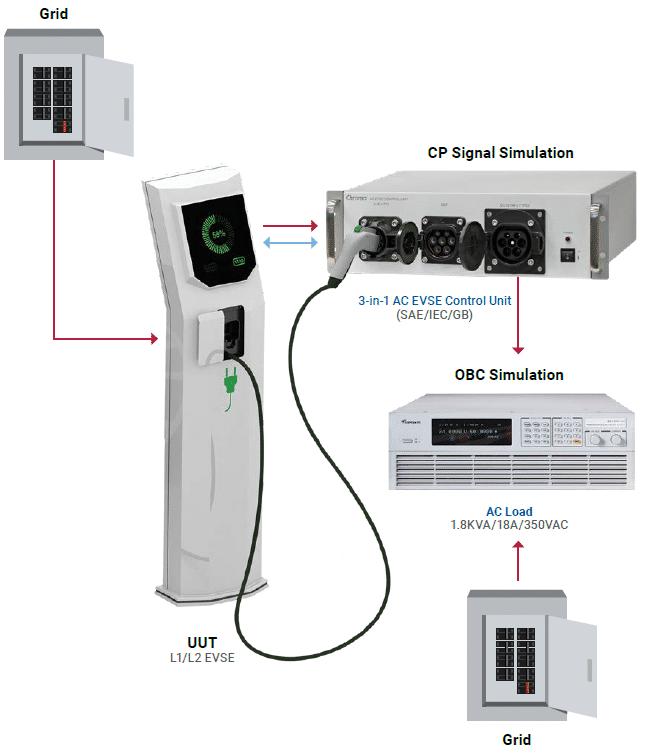
Test Cases
- Control Pilot Signal
- Abnormal Control Pilot Signal
- Current Capacity
- Couple Disconnection
- AC Energy Transfer
- Harmonic Distortion Immunity
- Voltage Interruption and Variation
- EVSE Invalid Test
- Input Output Test
SAE J1772 AC EVSE Test Cases
Control Pilot Signal Test
Control Pilot, commonly referred to as CP, is the PWM voltage signal that communicates the various states of the charging process between the EVSE and the EV; For example State A is disconnected, State B is vehicle that is connected, but not ready to charge, and state C is connected ready to charge. The CP signal test utilizes the Chroma AC EVSE control unit to simulate the expected, or normal, EV side CP signal relays and verifies that the EVSE is communicating per the related standards.
In the same regard, the Chroma AC EVSE control unit can simulate an abnormal CP signal where the PWM signal is out of range, or invalid, and evaluate how the charging system reacts to it. For SAE J1772, the test system utilizes the oscilloscope and digital multimeter to measure the control pilot of EVSE for voltage accuracy, frequency, and the rise and fall times.
Coupler Disconnection Test
The Chroma AC EVSE control unit is commanded to go to state A, which is the Static state, from any other state of charging or communication. Test the EVSE to put itself in a safe state which could be based on an internal or external fault, or when the couple is disconnected from the car during the charging process. Again, the digital multimeter is measuring the CP signal and the oscilloscope is measuring the time it takes to enter State A, which in this case is 100ms.
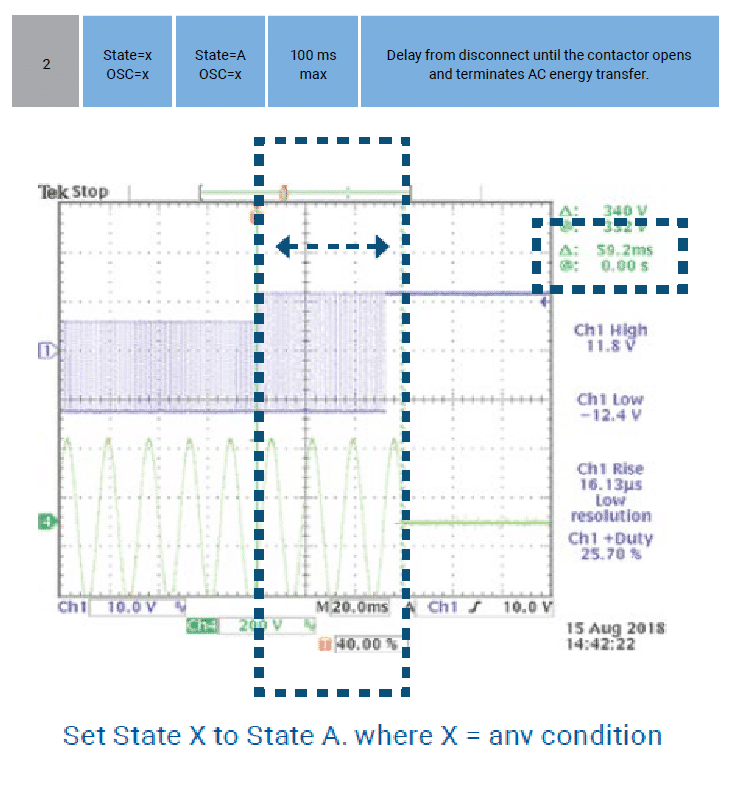
AC Energy Transfer Test
Another timing test, in this case the Chroma test system utilizes the AC EVSE control unit to switch from state B2 to state C or D, or alternately from state C or D to state B2. The Chroma Test System will utilize a scope to measure the delay time until the contactor closes, or in the latter case opens, and initiates AC energy transfer in response to the switching event, which needs to be 3 seconds or less per SAE J1772.
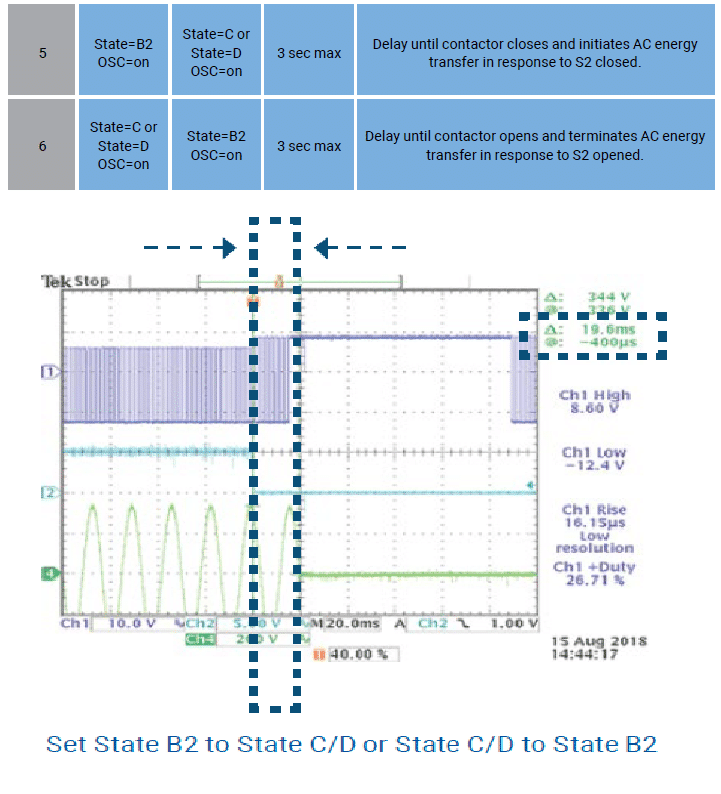
DC EVSE System
In a DC charging station, AC power provided by the AC grid is converted into DC power using a rectifier inside the DC charging station. The power control unit adjusts the voltage and current of the DC/DC converter inside the charging station to control the variable DC power delivered to charge the battery. There are safety interlock and protection circuits used to de-energize the EV connector and to stop the charging process whenever there is a fault condition or an improper connection between the EV and the charger.
The battery management system or BMS plays a key role of communicating with the charging station to control the voltage and current delivered to the battery and to operate the protection circuits in case of an unsafe situation. Note that the ISO and DIN specs utilize PLC communication while the GB and CHAdeMO specs utilize CANbus communication.
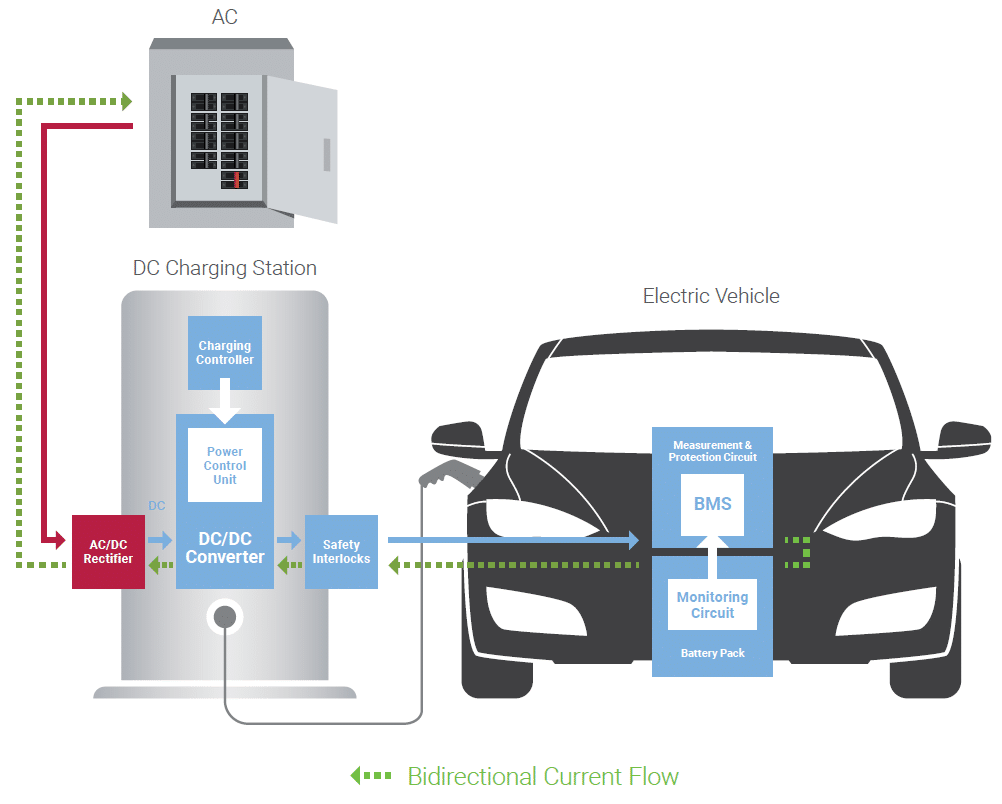
Key ATE Components for DC Fast Charging
The main and obvious difference between an AC L1/2 and a DC fast charger is that DC fast chargers put out DC power at the gun. Another major difference is that when using a DC fast charger, the EVSE charges the battery directly without requiring an OBC on the EV side.
Chroma’s DC EVSE test systems have 3 major components including a grid simulator which represents the input power to the EVSE, a DC EVSE Emulator which could be CCS or CHAdeMO, which handles all of the communication back to the charging station essentially simulating the EV. Finally, a battery simulator to accept the power from the charger to simulate the power to the battery.
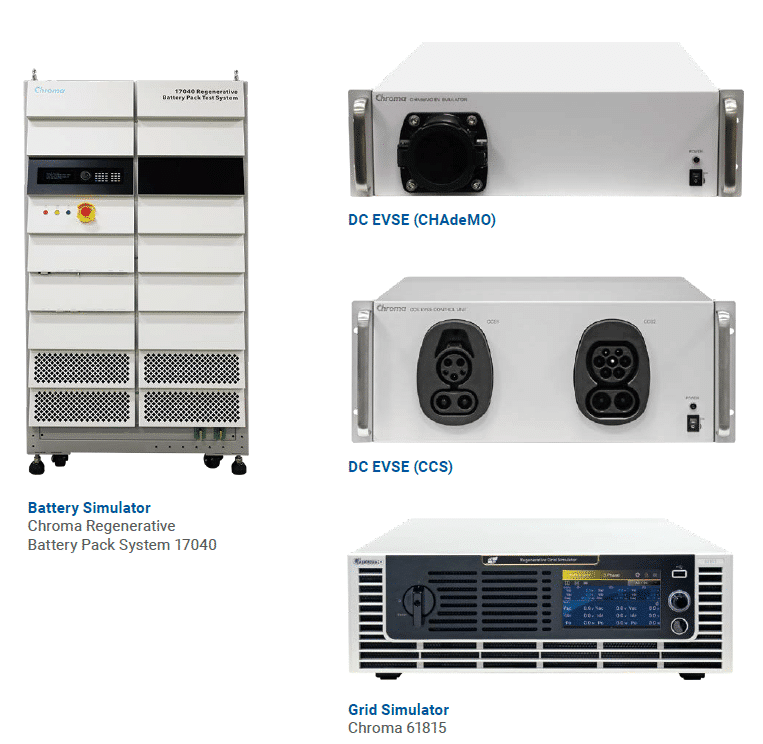
DC EVSE Test System
Chroma’s DC Fast Charger test system is very similar to the AC EVSE testers. It features a grid simulator, or an AC source, providing input power to the EVSE simulating test conditions such as line relation, peaks, surges, sags, power factor, etc. The Chroma DC EVSE control units which can be CCS, GB, or CHAdeMO simulates the BMS from the EV battery. The CCS EVSE control unit utilizes much of the same CP topology, but also incorporates a high Level communication protocol, specifically PLC or Power Line Communication. In a similar regard, both the GB and CHAdeMO EVSE Emulators utilize CANbus networks for a majority of their high and low level communication.
Differences
The most significant difference between the AC and DC EVSE’s is that DC EVSE’s incorporate additional layers of communication that enable smart charging which make it possible to perfectly match the grid’s capacity with the energy demand for the growing number of EVs that connect to the electrical grid. This additional communication layer also enables bidirectional energy transfer in order to realize vehicle-to-grid applications by feeding energy from the EV back to the grid when needed. It also provides an interface for “pay as you charge” secure payment applications which will help drive integration of DC Fast Charging into our global infrastructure. Standards like ISO 15118 allow for grid-friendly, secure, and convenient charging of EVs.
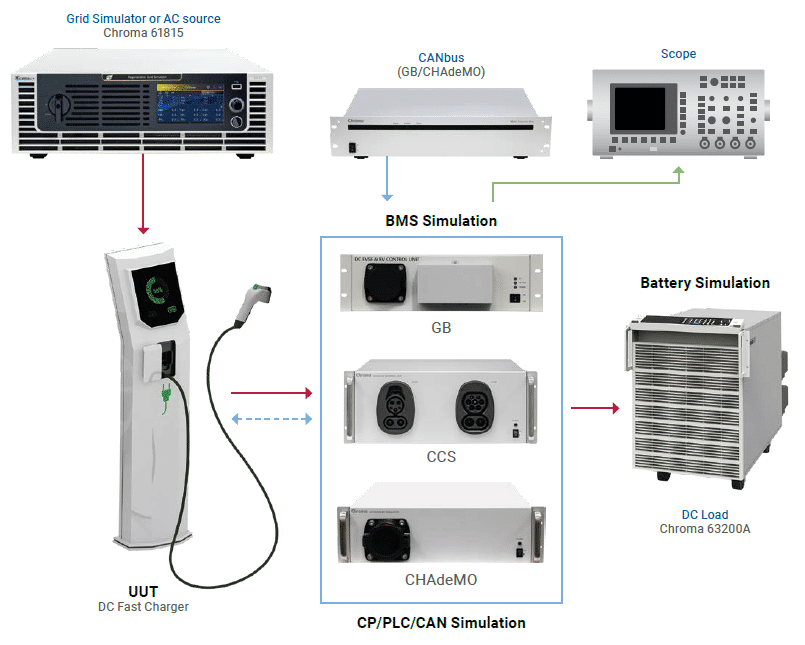
Standard Tests
- SAE J1772
- ISO 15118
- GB/T 18487.1
- GB/T 34657.1
- GB/T 27930
- GB/T 34658
- IEC61851-1
- CHAdeMO
- DIN 70121/2
Bi-directional DC EVSE Test System
A bidirectional DC EVSE test system incorporates a grid simulator on the input side to the EVSE, and replaces the DC load with a battery simulator on the opposite end. This test system can be designed to be regenerative, which provides a high rate of efficiency as compared to the source / load configuration. There is no question that vehicle-to-grid charging is going to be a widespread application in the future. So the question is: Do you invest in a system that will meet your needs today, i.e. source and load? Or do you invest in a more capable system utilizing a grid simulator and a battery simulator to make sure that you are protected for the future?
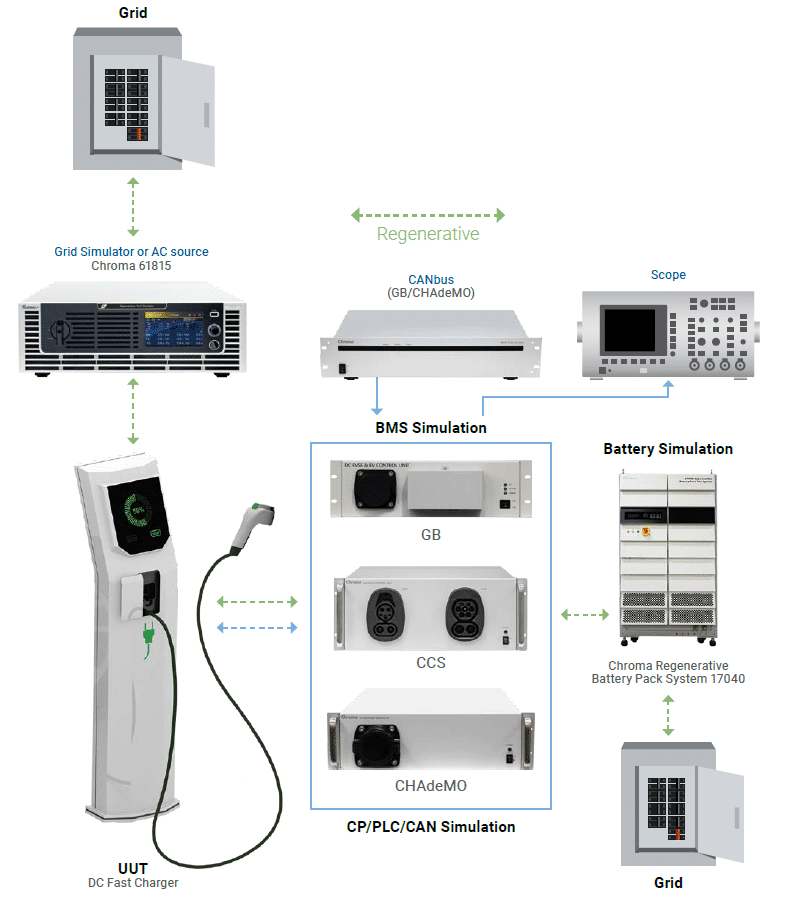
EVSE Interoperability Test System
majority of the interoperability tests and related standards are common with those applicable to the EVSE test systems. Components include: grid simulator or alternately a DC source, depending on whether it is an AC or DC application. The next component is the EVSE emulator which simulates the EVSE CP and PLC signals. As part of the charging system, the OBC will need to see the same high and low level signals that would be produced by the EVSE in order to operate.
Finally, there is the AC/DC charging control unit. Think about this as the traffic controller for power and communication to or from the EV. This unit also provides an easy access interface for measurement of power, as well as timing measurement for communication signals required for the time based tests.
Key ATE Components
Interoperability Tests
- Loading Current Correction test
- Proximity Circuit Opening test
- Harmonic Distortion Immunity test
- Voltage Dips, Short Interruptions and Variations Immunity test
- EVSE Invalid test
- Control Pilot Simulation test
Available Test Standards
- GB/T18487.1, 27930, 34657, 34658
- ISO15118
- IEC61851-1
- CHAdeMO
- DIN 70121/2
- SAE-J1772
- CNS15511
AC L1/L2 EVSE Interoperability Test System
In an AC EVSE Interoperability system, there is no PLC communication required. The Chroma EVSE signal emulator simulates the CP signals for the EV to start and finish the charging process. The digital multimeter and oscilloscope measures the CP signals between the EVSE control unit and the EV for compliance with SAE J1772.
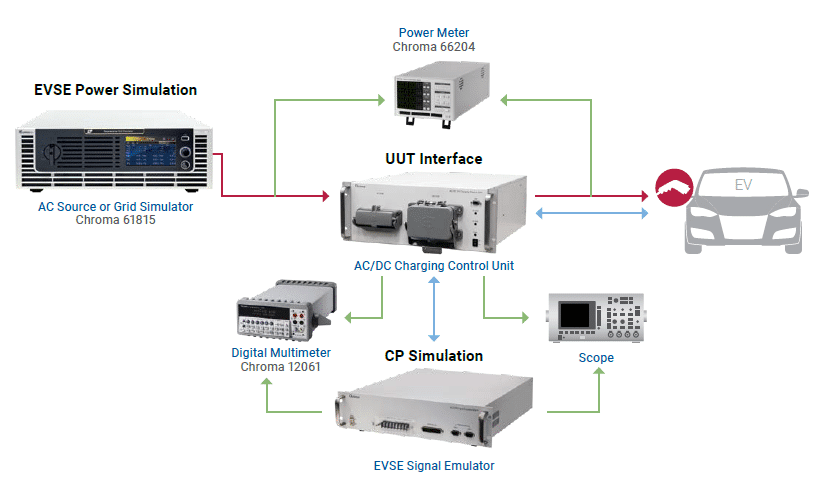
DC CCS EVSE Interoperability Test System
One key difference between the AC EVSE interoperability test system and the DC test system is the addition of the DC EVSE emulator. CCS testing requires the implementation of the PLC signals for high level communication for a DC fast charge system. Another important feature of the DC CCS EVSE emulator is that it contains all of the industry standard ISO and IEC test procedures required for verification. Some DC Fast Chargers require a cooling system to keep temperatures down in the transmission lines.
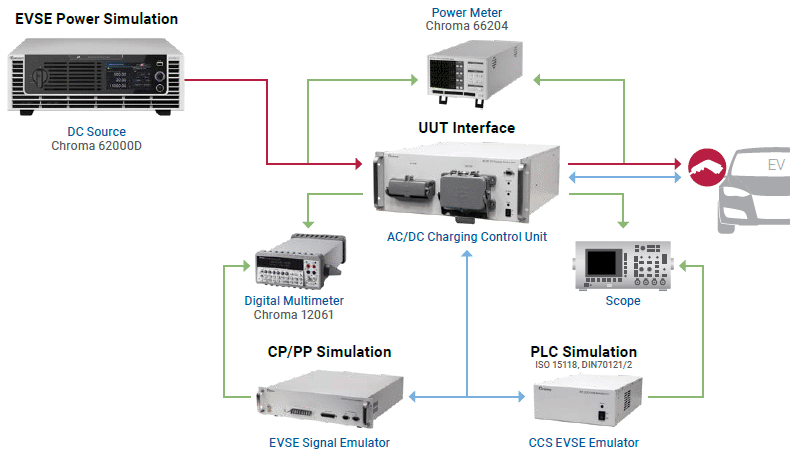
MORE FROM THE MEDIA HUB
February 2, 2024
Future Propulsion Conference 2024
READ MOREJanuary 15, 2024
A dedicated resistance meter? Here is when it makes sense…
READ MOREDecember 4, 2023